This piece was originally written for the Tender Stores newsletter. If you would like to sign up for our occasional mailing list please
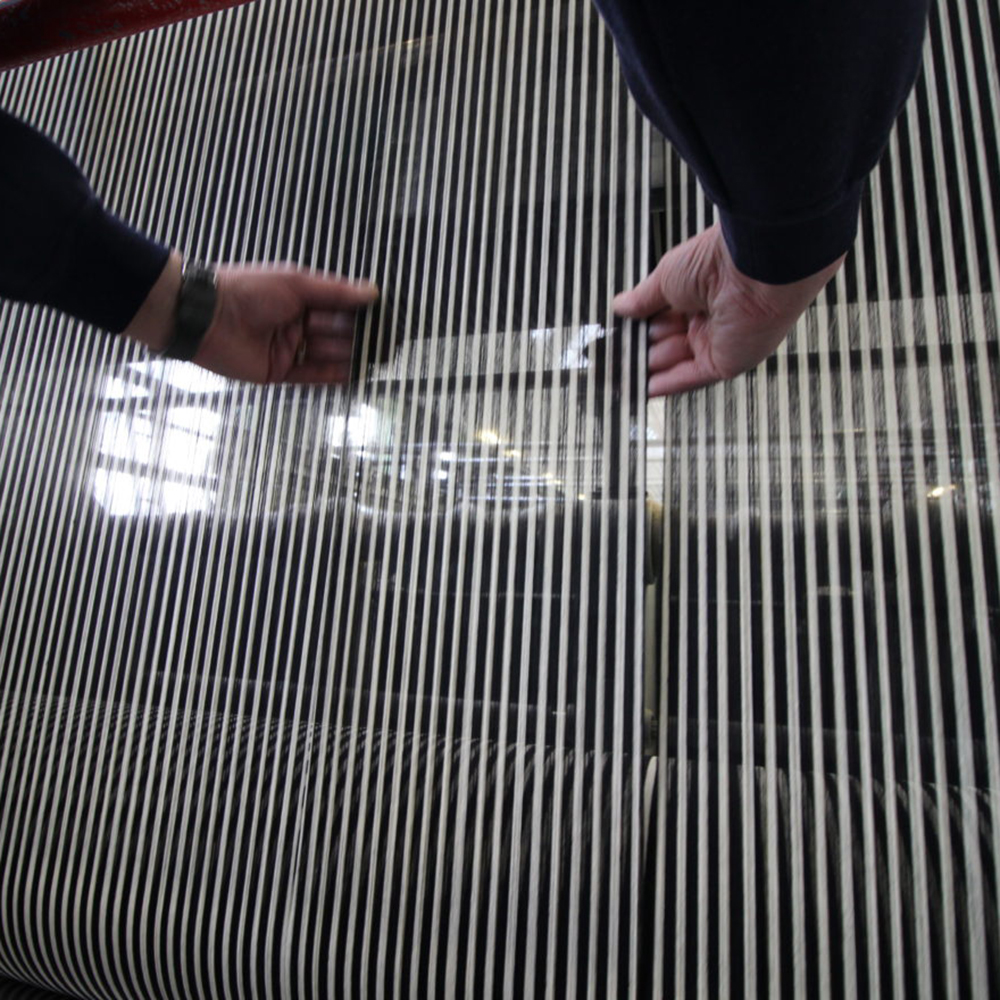
On Woven Stripes
A stripe is one of the simplest patterns that can be woven into a piece of fabric, but the design and manufacturing decisions that go into stripes can be quite interesting. In this piece I’ll write a bit about striped fabric design, and how I’ve used it for Tender garments over the years.
Woven fabric comprises a warp, a set of yarn threads which run along the length of a piece of fabric, and a weft (I was taught to remember that weft rhymes with left, as in left to right, which is a bit silly but has stuck in my head), meshed together one way or another on a loom. The warp yarns are called ends and the weft yarns are called picks. On a shuttle loom (such as produces selvage denim) the weft is carried side to side across the warp inside a wooden shuttle, so the picks are made up of the same length of unbroken yarn. On a rapier loom, used for wider fabrics, a cone of weft yarn sits at the side of the loom and picks of weft yarn are shot across the warp and cut off before the warp advances and the next pick is shot across. The entire warp is prepared before weaving can begin (a process I go into in a superfuture post from a few years ago, which you can find here), and is a pretty involved job. Due to the run-on and run-off wastage you have to commit to a fairly large amount of fabric, and once you’ve set up a warp, all the fabric that comes off it will have the same warp pattern. This sounds like an obvious point, and really it is, but rather like the apocryphal request that every dyer seems to have had to dye checks it’s not completely obvious unless you understand how it works.
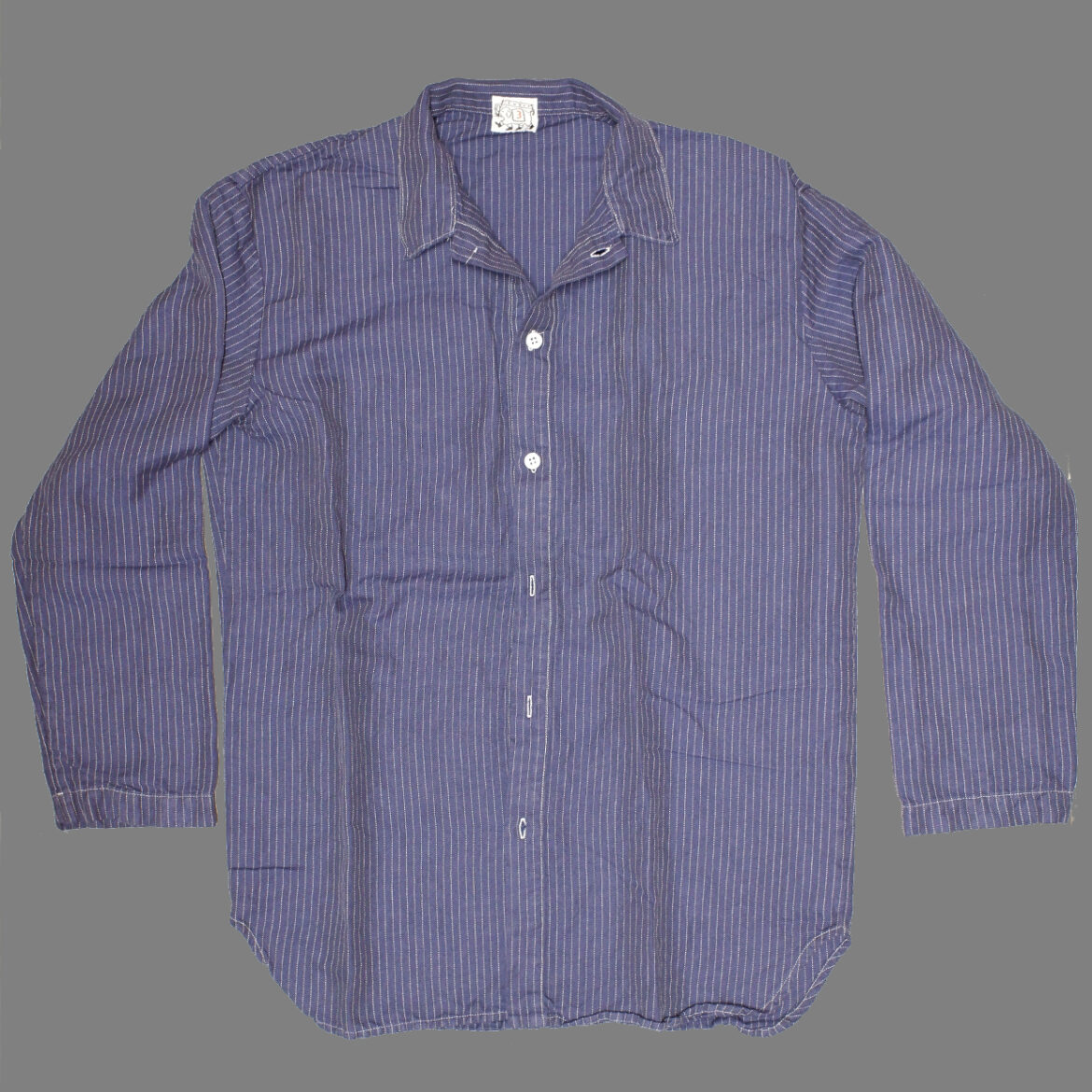
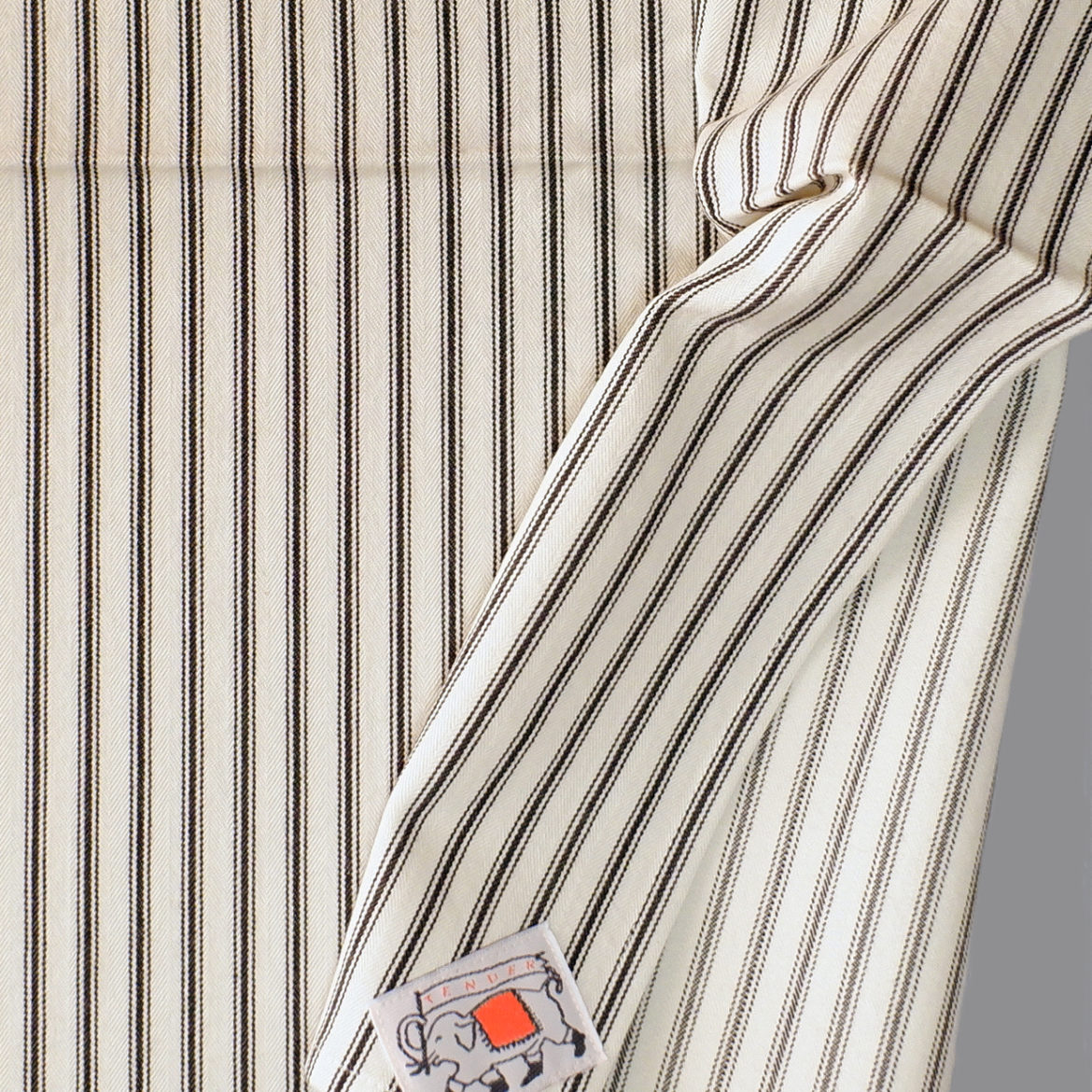
The first stripes I introduced within Tender were stock upholstery ticking stripes. This was before I was able to order enough fabric to be able to design and commission my own fabrics, and tickings are technically very nice cloths, with a particular vernacular British quality which seemed to work well for shirts. Tickings are tightly woven, often in a herringbone pattern, to keep upholstery pads and layers of horsehair wadding securely in place so that a fancier top fabric doesn’t have bits of hair and feathers sticking through it. The original purpose of the stripes was to allow the upholsterer to keep the fabric straight over the frame- when cloth is being stretched and steamed tight onto a complicated shape like an armchair it can be tricky to keep track of the grain, and an uneven underlayer of fabric could cause bagginess or creasing in the top layer once the fabric settles. A classic ticking fabric actually has two different stripes- a yarn stripe, (the obvious coloured stripe which is set up on the warp) and a weaving stripe, which is the textural herringbone stripe that sits between the coloured stripes. While the yarn stripe is fixed for the entire length of the warp, the weaving stripe is a result of the weaving technique, and can be altered within the piece.
At the most basic level there are two weaving patterns: plain weave, where the warp and weft cross each other in a 1:1 ratio; and a twill, where the weft crosses several warp yarns at a time, before crossing underneath, causing a diagonal ridged (twilled) texture on the face of the fabric. The twill can run diagonally from top right to bottom left (right hand twill) or from top left to bottom right (left hand twill). The twill direction on the back of the fabric runs in the opposite direction to the front. The pitch of the twill can be altered depending on the ratio of warp ends crossed by a weft pick before switching sides, and the twill can be varied during the piece to create a broken twill (a pick’s worth of right hand twill, followed by a pick’s worth of left hand twill) or a herringbone (the same idea, just spread out a bit with repeats), or more complicated designs.
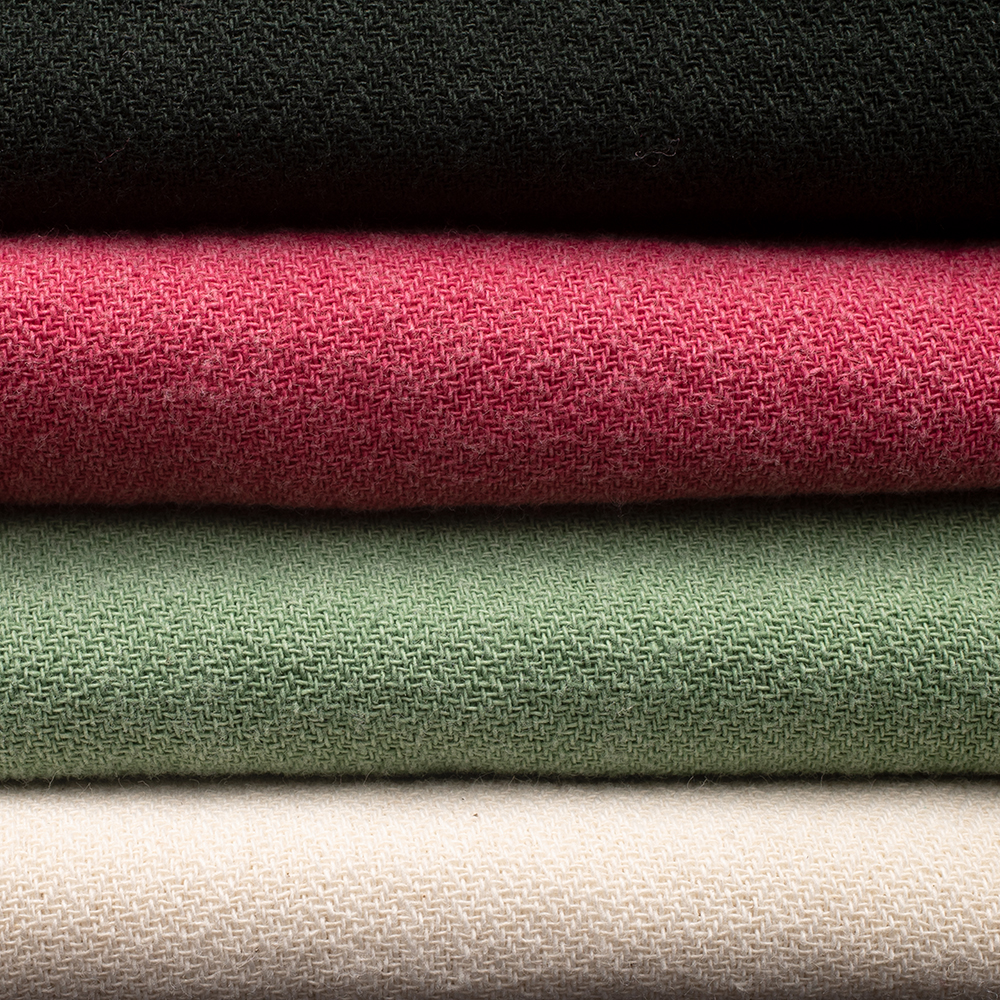
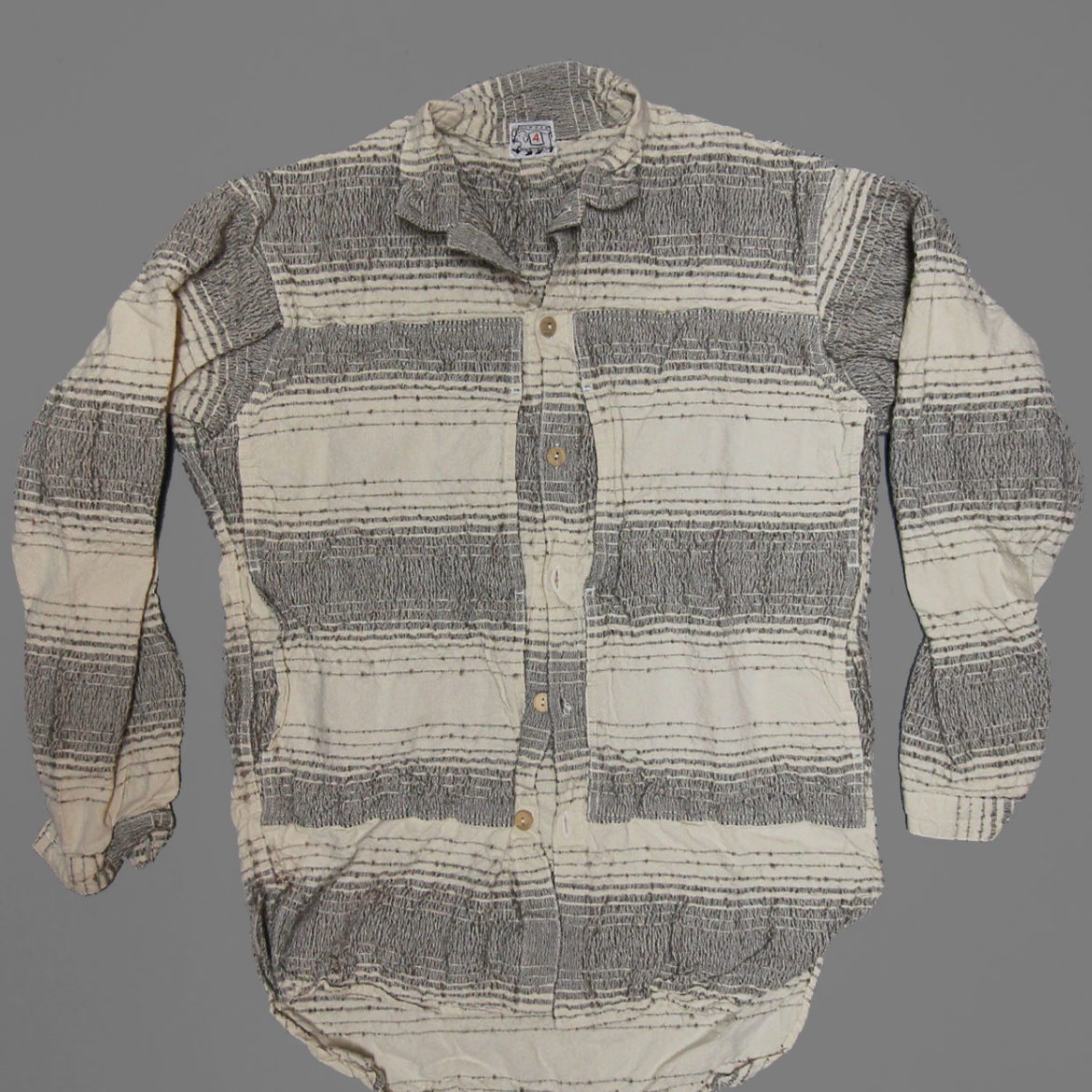
A weft yarn stripe can be created on a plain warp, which will produce sideways contrasting stripes on the fabric, or on a striped warp, which will produce a plaid or gingham check. The weaving pattern can also be set up to make a weft weaving stripe, forming textured bands in the same yarn across a piece of fabric. The advantage to me, as the owner of a very small brand, of horizontal stripes is that various different fabrics can be woven on the same warp, without committing an entire warp length to one quality. Experimenting with weft stripes has become a big part of Tender’s textile identity. Here follow some examples, and how they came about.
Ryeland Wool Doppler Stripe Calico was woven on a plain ecru cotton warp, in weft bands of the same ecru cotton and much thicker natural grey Ryeland wool. The slubs in the wool picks form dots in the lines, and the wool shrinks more than the cotton when the garment is rinsed or dyed, causing it to pull in and pucker.
Tablecloth Stripe was based on a checked tablecloth that I remember from my great aunt’s house. It was a checkerboard pattern (with clear on/off checks, unlike the half tones in a gingham or plaid), which must be woven as a double faced fabric, or on a jacquard loom (a whole nother thing!) This striped version is a blue and white double cloth- a stripe that shows blue on the face is white on the reverse, and the structure of the fabric creates channels in the stripes, trapping air inside and making the shirt particularly soft and comfortable to wear.
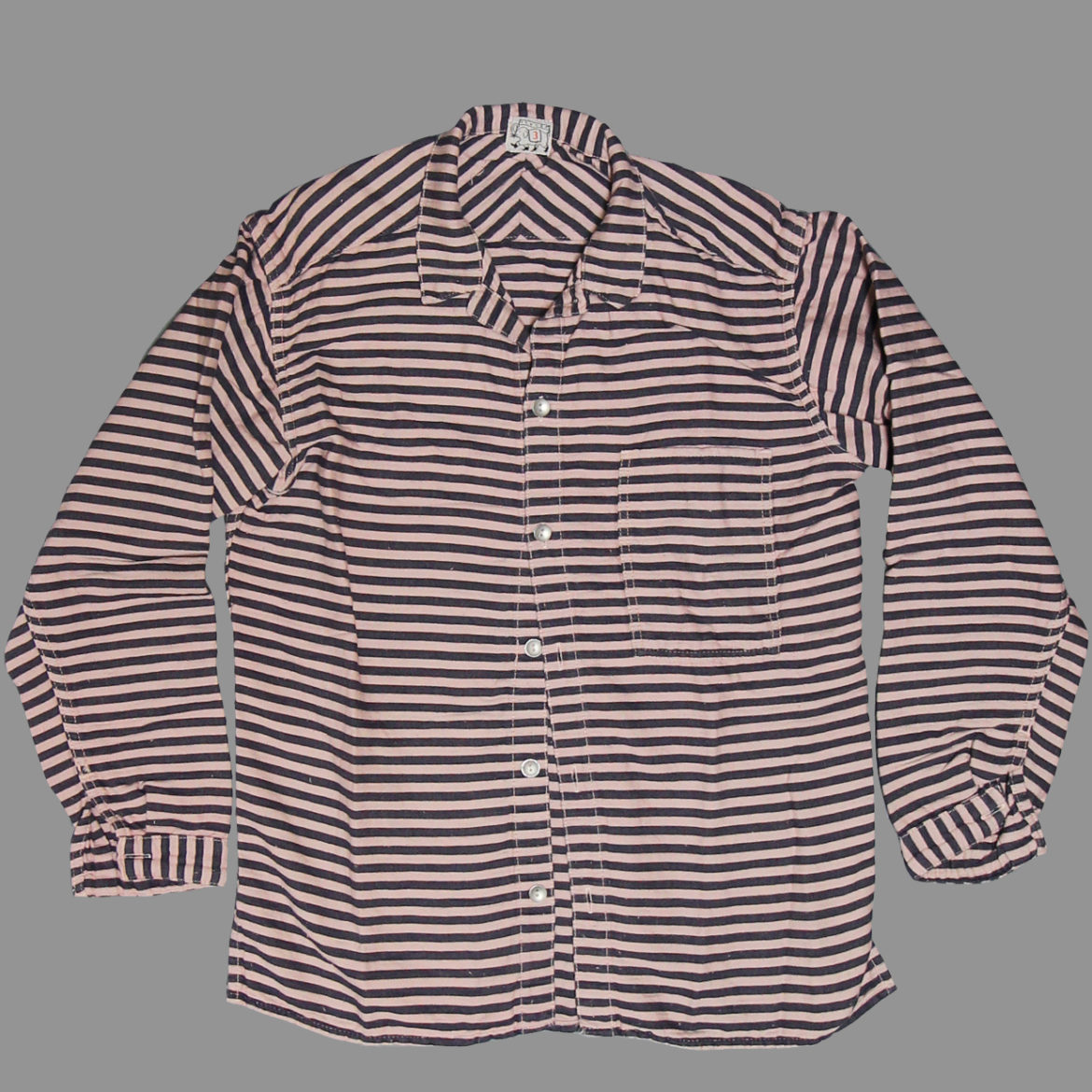
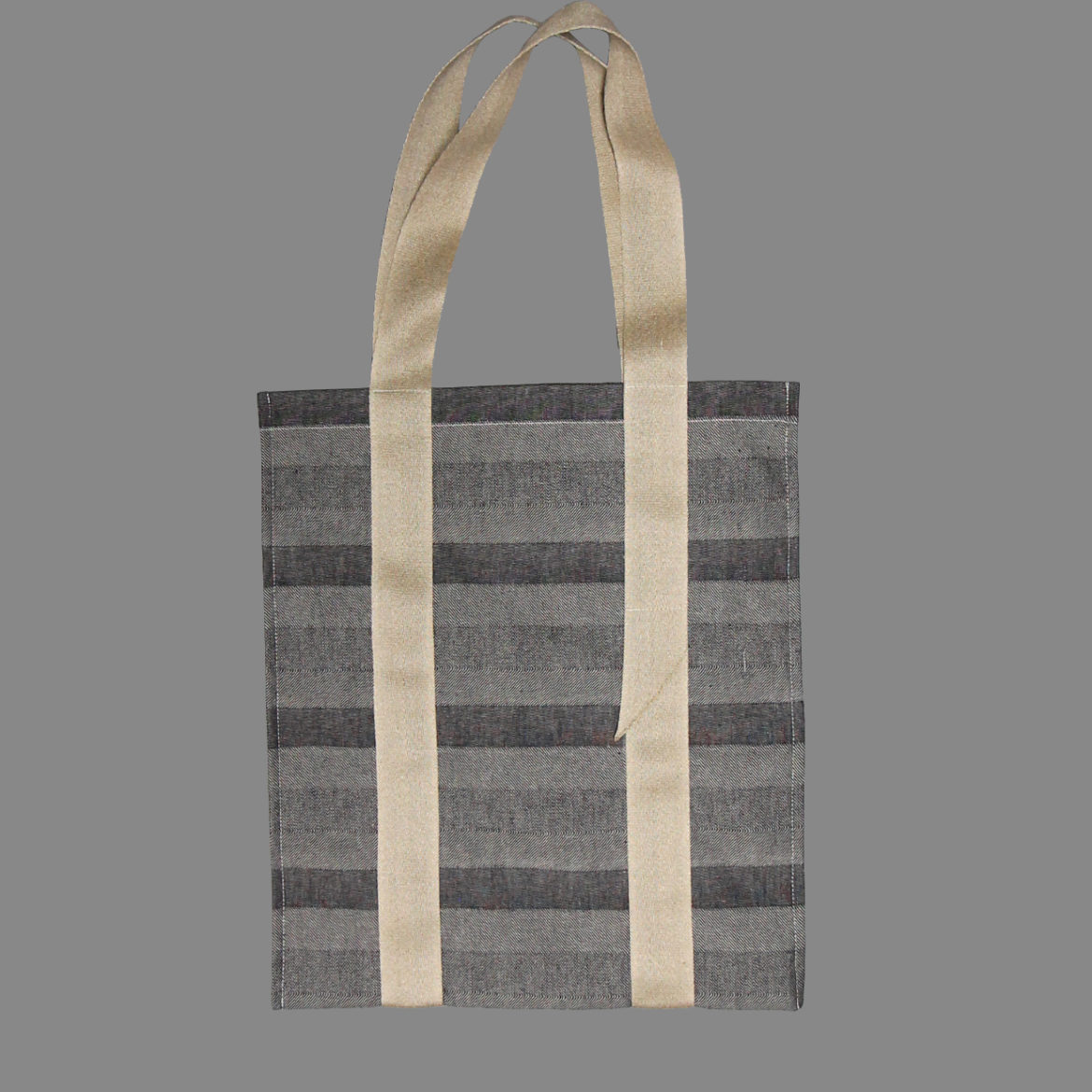
Indigo Weaver’s Blanket Stripe is woven on a solid indigo cotton warp with an ecru weft, like a standard denim, however the twill switches every hundred picks or so, between a right hand twill, a plain weave, a left hand twill, and a broken twill. The same weaving pattern with added yarn stripes of indigo as well as the weaving stripes makes the Bold Indigo version of this fabric.
Chain Cord is a woven warp stripe, created on a plain ecru warp with raised warp ends forming the ridges along the fabric. When an indigo weft is used in the same pattern, the cords show up white over a blue background. The structure of the fabric creates a differential shrinkage, making the puckered texture between the cords, and pulling shirts made of it in to a slim fit.
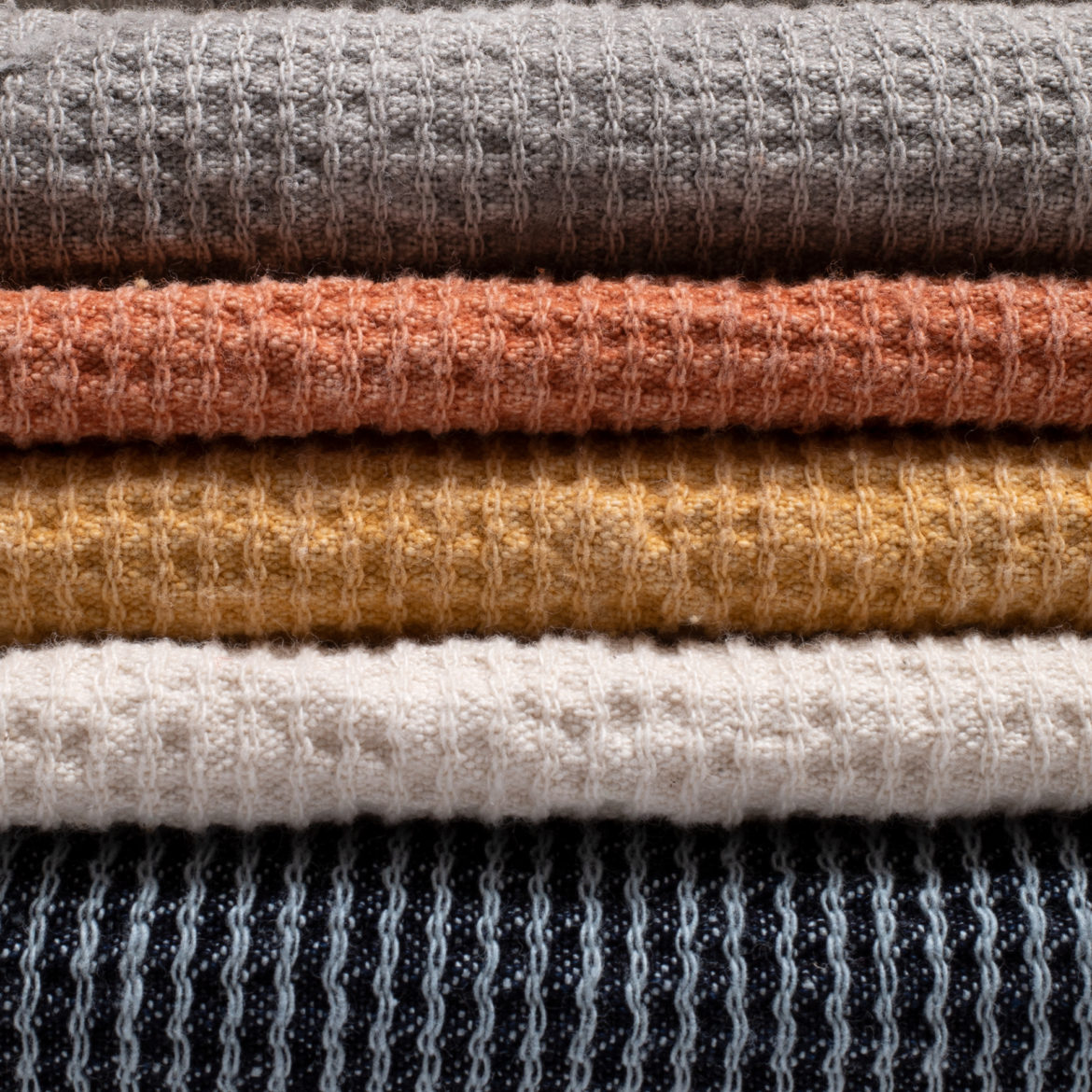
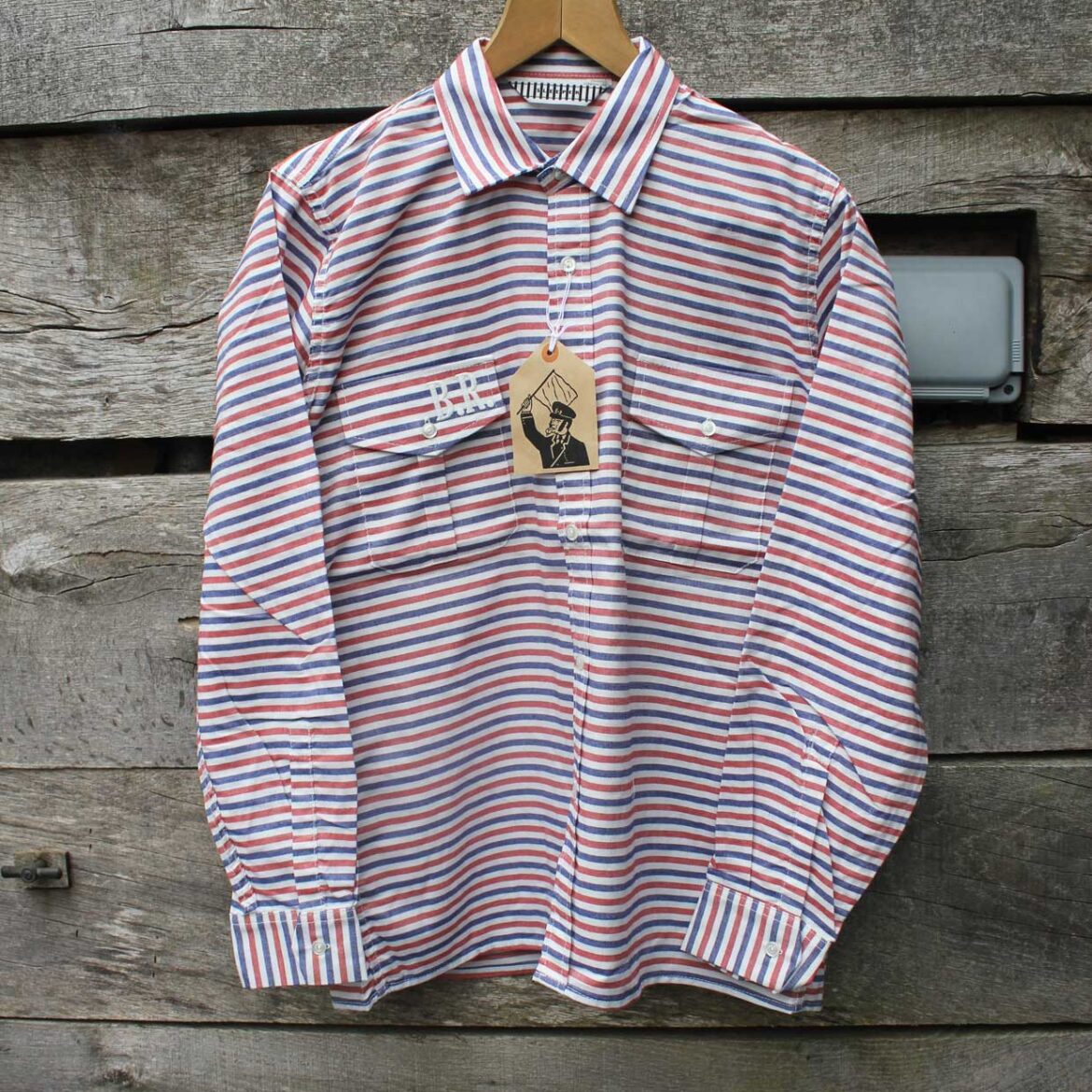
Sleeper shirts are made in Japan using Japanese fabrics and vintage British Rail uniform patterns. This Tricolore Bengal Stripe is a fine cotton poplin, like a traditional dress shirt, but woven with the stripe in the weft, rather than the warp, giving a very different effect.
This piece was originally written for the Tender Stores newsletter. If you would like to sign up for our occasional mailing list please